Wann ist Automatisierung in der Intralogistik die beste Wahl?Innerbetriebliche Prozesse kostengünstiger und effizienter gestalten
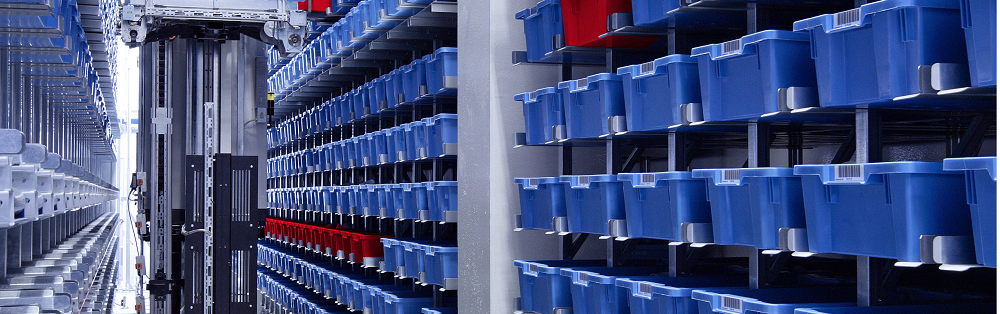
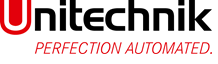
Die Entscheidung für oder gegen eine automatisierte Lösung ist oft geprägt von Vorurteilen: Automatisierung punkte mit höherer Geschwindigkeit und besserer Platzausnutzung bei niedrigeren Betriebskosten, erfordere aber eine hohe Investition und mache die Logistik unflexibler. Doch treffen diese vermeintlichen Vor- und Nachteile wirklich zu? Um das zu beantworten, sollten sich Verantwortliche mit den Herausforderungen und Chancen des Einsatzes auseinandersetzen.
Der industrielle Mittelstand ist zwiegespalten: Einerseits möchte er die kontinuierlich steigenden Ansprüche der Kunden hinsichtlich kleinerer Losgrößen und kurzer Lieferzeiten erfüllen können, andererseits aber auch auf aufwändige und kostspielige Eingriffe in die bestehende Lagerinfrastruktur verzichten. So steigt der Automatisierungsgrad in der innerbetrieblichen Logistik deutscher Unternehmen zwar immer weiter, ist aber insgesamt noch auf einem niedrigen Niveau, wie eine kürzlich durchgeführte Studie der Firma Unitechnik zeigt. In manchen Fällen liegt das an einem mangelnden Bewusstsein für das Optimierungspotenzial durch die Automatisierung von Prozessen, oft aber auch an Vorurteilen rund um die Implementierung. Zu teuer, zu aufwändig, zu unflexibel erscheint die Automatisierung vielen Verantwortlichen in der Intralogistik. Hier lohnt jedoch ein zweiter Blick.
Teure Anschaffung vs. geringere Betriebskosten
Es stimmt: Für die Anschaffung und Inbetriebnahme einer automatisierten Lösung sind höhere Investitionskosten erforderlich als bei einer manuellen Lösung. Wie hoch die Kosten tatsächlich ausfallen, ist vom Automatisierungsgrad abhängig. Dabei gibt es nicht nur schwarz oder weiß. Sinnvoll ist die intelligente Mischung von automatisierten, teilautomatisierten und manuellen Arbeitsschritten, um mit möglichst wenig Aufwand die gewünschten Ziele zu erreichen. Die konkrete Ausgestaltung sollte Teil eines vorausgehenden Planungsprozesses sein. Doch die Investition ist nur eine Seite der Medaille. Die anfänglich hohen Kosten amortisieren sich nach einer gewissen Zeit: Die höhere Durchsatzleistung ohne zusätzliches Personal führt – insbesondere bei einem Mehrschichtbetrieb – zu geringeren Stück- und Betriebskosten. Auch der geringere Flächenverbrauch durch die automatisierte Logistikanlage macht sich positiv bemerkbar.
Flexibel – trotz fester Infrastruktur
Um mit den beschleunigten Prozessen Schritt zu halten, suchen Intralogistiker nach leistungsfähigen Lösungen, die flexibel und skalierbar sind. Automatisierte Lager stehen aber in dem Ruf, aufgrund ihrer festen Infrastruktur das genaue Gegenteil darzustellen. Es ist zwar richtig, dass man bei einem automatisierten Logistiksystem mit definierten Ladungsträgern arbeitet. Da Behälter oder Paletten feste Abmessungen und ein maximales Gewicht haben, ist die nachträgliche Änderung des Artikelspektrums mitunter eingeschränkt. Durch eine intelligente Gestaltung der Lösung lassen sich jedoch bereits zahlreiche Zukunftsszenarien abbilden. Beispielsweise hat sich die Kombination von einem Palettenhochregallager und einem Automatischen Kleinteilelager bewährt. Außerdem lassen sich mittels Tablaren Lösungen entwickeln, die eine hohe Flexibilität ermöglichen.
Skalierbare Lösung mit effizienter Platzausnutzung
Eine gewisse Skalierbarkeit erreicht man bei Lagersystemen, die von Shuttle-Fahrzeugen bedient werden. Über die Anzahl der Fahrzeuge kann die Leistung an gestiegene Anforderungen angepasst werden. Selbst klassische Lager mit Regalbediengeräten erlauben eine nachträgliche Leistungserhöhung durch das Nachrüsten eines zusätzlichen Lastaufnahmemittels. Hinsichtlich der Leistungsfähigkeit punkten automatisierte Systeme mit Geschwindigkeit und hoher Kapazität. Da es in einer automatisierten Umgebung unabhängig von der Größe des Artikelspektrums nur wenige Minuten dauert, bis die Ware beim Kommissionierer ankommt, entsteht ein sehr schneller Auftragsdurchlauf. Zudem erhöhen automatisierte Lösungen in der Regel die Lagerkapazitäten: Automatische Hochregallager, die bis zu 45 Meter hoch sind, nutzen die Fläche effizient – vor allem bei mehrfachtiefer Lagerung. Durch Automatisierungs- und Assistenzsysteme lassen sich Kommissionierfehler reduzieren, die Verpackungsqualität verbessern und damit die Lieferqualität optimieren. Das Ergebnis: zufriedene Kunden und weniger Retouren.
Instandhaltung wird zum Erfolgsfaktor
Durch den Einsatz einer automatisierten Logistikanlage benötigt man keine Mitarbeiter mehr – so ein weit verbreiteter Irrglaube. Gerade die Mitarbeiter sind jedoch ein entscheidender Faktor, wenn es um den Erfolg oder das Scheitern der Automatisierung geht. Das gilt insbesondere für die Instandhaltung. Denn die Anlage kann – wie jede Art von Technik – ausfallen. Hier ist geschultes Personal gefragt, das sich mit der Funktionsweise und möglichen Störungsursachen auskennt. So kann es Störungen schnellstmöglich beheben und eine möglichst hohe Verfügbarkeit der Anlage gewährleisten. Assistenzsysteme wie Störungsanalysetools und Anlagenvisualisierung zum Status der Anlage und ihrer Komponenten unterstützen dieses Ziel. Kommt der Instandhalter nicht zurecht, können die Spezialisten des Anlagenlieferanten per Fernzugriff helfen. Auch mit präventiven Hinweisen an die Logistikmitarbeiter auf Bedienungsfehler oder unsachgemäßes Beladen – als häufige Ursachen für Störfälle – verbessert die Instandhaltung die Zuverlässigkeit der Anlage.
Ein gutes Anlagendesign ist die beste Voraussetzung dafür, dass Service und Reparatur schnell gelingen.
Automatisierte Systeme unterstützen Mitarbeiter
Die Logistikmitarbeiter arbeiten mit technischen Geräten wie Datenbrillen und Pick-by-Voice-Geräten. Dadurch werden sie von der Technik unterstützt, müssen aber auch mehr Vorgänge in der gleichen Zeit schaffen. Großbildschirme, die wichtige Kennzahlen anzeigen, motivieren die Mitarbeiter dabei, da sie so in die Gesamtprozesse einbezogen werden. Auch der Lagerleiter profitiert: Das Lagerverwaltungssystem (LVS) liefert ihm alle Informationen zu Aufträgen, Beständen und Anlagenzustand. Über umfangreiche Analysetools kann er Engpässe erkennen, bevor diese zum Problem werden. Mobile Endgeräte und eine übersichtliche Anlagenvisualisierung helfen ihm dabei, den Betrieb zu führen und kontinuierlich zu optimieren.
Heutzutage spielt auch die Ergonomie am Arbeitsplatz eine große Rolle. Eine automatisierte Anlage kann hier einen guten Beitrag leisten: Das Material wird zum Beispiel automatisch angedient; Artikel- und Auftragsbehälter sind so angeordnet, dass Abstände, Bewegungsabläufe und Greifhöhen den Mitarbeiter möglichst wenig belasten. Diese Aspekte können bereits in der Planungsphase berücksichtigt und mittels Virtual Reality getestet werden – entsprechend den jeweiligen Bedürfnissen. Zudem trägt das automatisierte Logistiksystem zu einem verbesserten Arbeitsschutz bei. Mögliche Unfallrisiken wie Staplerverkehr werden reduziert. Automatisierte Systeme können in widrigen Umgebungen, zum Beispiel im Tiefkühllager, menschliche Tätigkeiten übernehmen.
Die wirtschaftlichste Lösung finden
Fest steht: Automatisierung kann ein wichtiger Wettbewerbsfaktor sein, um die steigenden Kundenanforderungen in puncto Lieferqualität und Reaktionszeiten, bei gleichzeitigem Kostendruck, zu erfüllen. Ob und in welchem Maße die beschriebenen Vorteile für ein Unternehmen relevant sind, hängt vom Einzelfall ab. Damit die Entscheidung für eine passgenaue Lösung aus einer Vielzahl von möglichen Varianten gelingt, empfiehlt sich eine strategische Herangehensweise. Bevor die Investitionsentscheidung fällt, zeigt eine Planungsphase mit externer Unterstützung, zum Beispiel durch einen Generalunternehmer wie Unitechnik, den optimalen Weg für den eigenen Betrieb auf – ob nun manuell, teilautomatisiert oder hochautomatisiert.
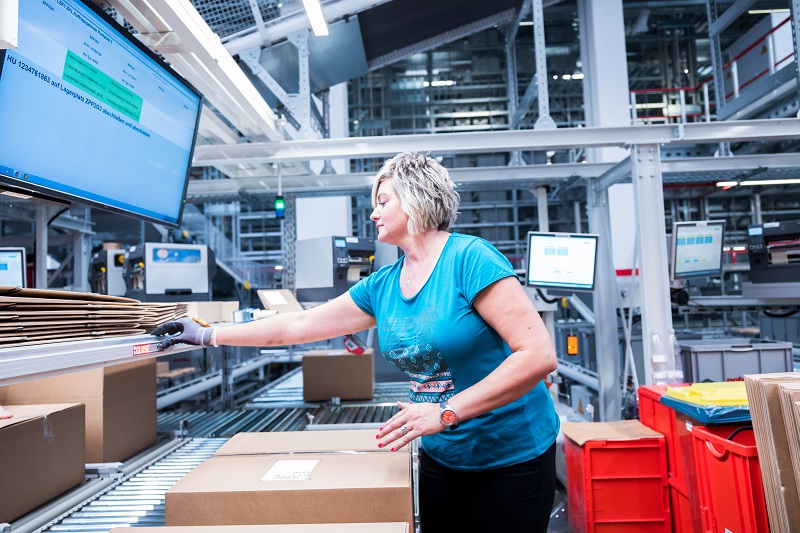
Logistikmitarbeiter in einer automatisierten Anlage arbeiten mit einer Vielzahl von technischen Geräten. © Unitechnik Systems GmbH
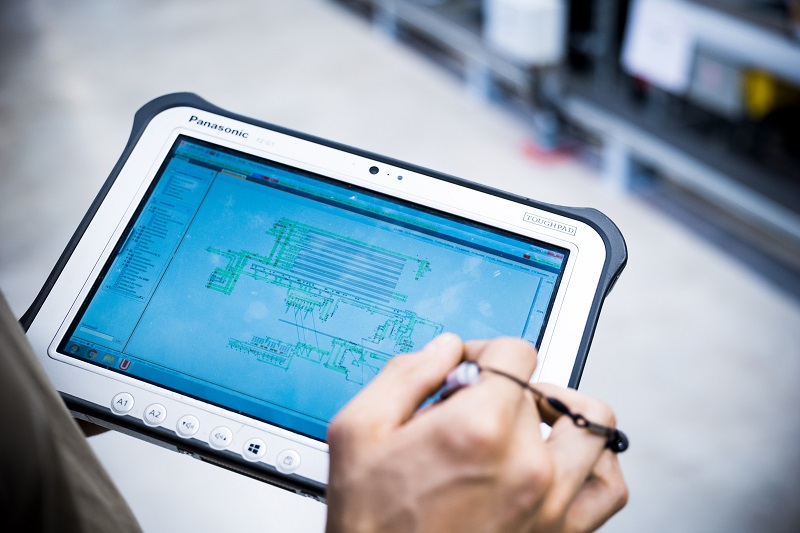
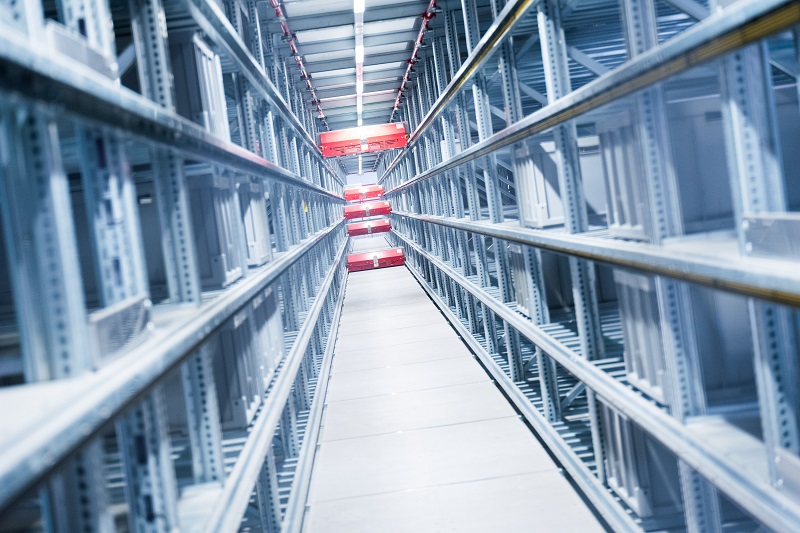
Eine gewisse Skalierbarkeit erreicht man bei Lagersystemen, die von Shuttle-Fahrzeugen bedient werden. © Unitechnik Systems GmbH
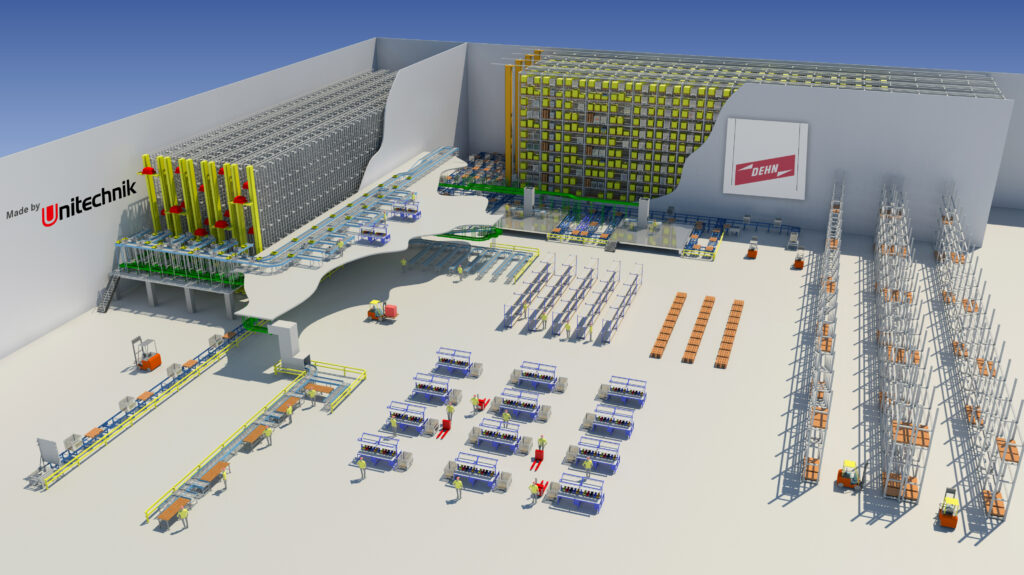
In der Planungsphase wird eine passgenaue Lösung aus einer Vielzahl von möglichen Varianten entwickelt. © Unitechnik Systems GmbH
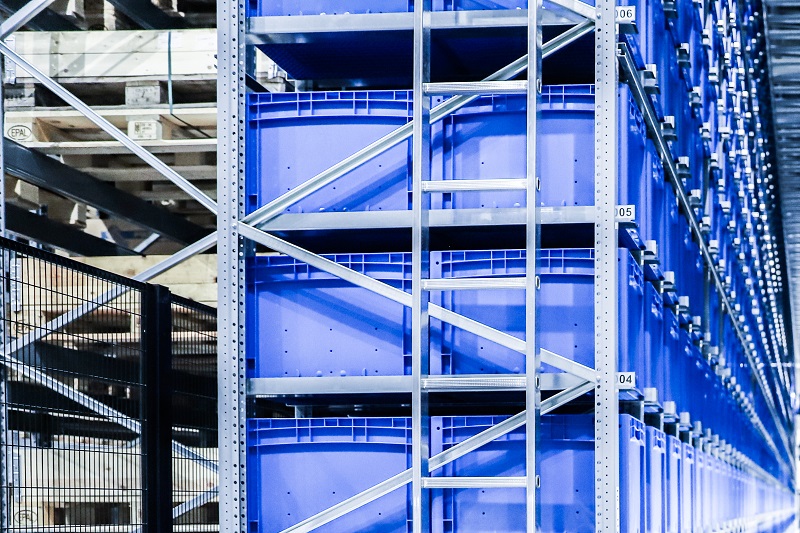
Quelle: www.unitechnik.com
Foto „head“: Automatisierung punktet mit höherer Geschwindigkeit und besserer Platzausnutzung bei niedrigeren Betriebskosten.
Schlagwörter: Unitechnik