„Unsere Kunden müssen unter reinen Bedingungen fertigen“Interview zur Motek mit Ulrich, Moser, Leitung Marketing & Vertriebscontrolling bei IEF-Werner
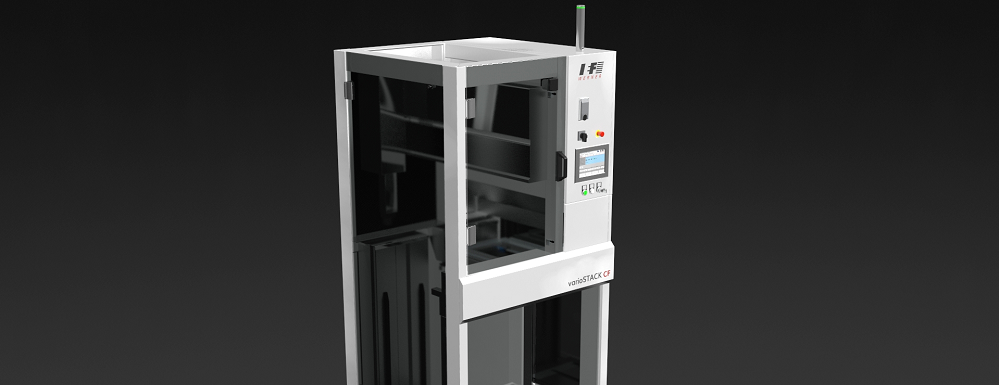
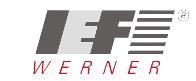
Die Motek feiert in diesem Jahr ihr 40. Jubiläum. IEF-Werner ist Aussteller der ersten Stunde. Welche Bedeutung hat diese Messe für Sie?
Wir sind von Anfang an dabei. Diese Fachmesse ist für uns ein ausgezeichnetes Schaufenster der wirtschaftlichen Leistungsfähigkeit der Montage- und Automatisierungstechnik. Sie hat sich für uns sehr schnell zum Messe-Highlight des Jahres entwickelt. Wer heute wissen möchte, welche Neuheiten es in der Branche gibt, erfährt es live in Stuttgart. Die Motek hat maßgeblich dazu beigetragen, dass sich die Branche wie auch unser Unternehmen entwickelt hat. Die Messe ist für uns heute mehr denn je die wichtigste Plattform, um Bestands- und potenziellen Neukunden unsere Innovationen vorzustellen. Und das wird sie in dieser innovativen Branche auch weiterhin bleiben.
Ein Messeschwerpunkt war unter anderem der varioSTACK CF „Clean Factory“. Was zeichnet dieses System aus?
Das offene und modulare Palettiersystem eignet sich für hochgenaue und automatisierte Fertigungsprozesse in Reinräumen. Unsere Kunden in der Medizintechnik, in der Pharmabranche und in der Elektroindustrie setzen dieses ganzheitliche Palettierer-Konzept erfolgreich ein. Wir passen es an nahezu jede Aufgabenstellung an. Der Anwender kann den äußerst kompakten Palettierer mit einem integrierten IEF-Produkthandling betreiben und standardmäßig mit Palettenwagen oder Transportbändern beladen. Es lassen sich Trays mit einem Gewicht von bis zu 15 Kilogramm ein- und ausschleusen.
Sie haben diese Maschine hinsichtlich Partikelgenerierung und Abreinigbarkeit optimiert. Kamen die Anforderungen vom Markt?
Die Anforderungen an unsere Kunden an eine saubere Produktion werden immer höher. Sie müssen ihre Fertigung daran anpassen. Um sie dabei zu unterstützen, haben wir beim varioSTACK CF unter Beibehaltung der schnellen Taktzeiten speziell die Aspekte der Partikelgenerierung und Abreinigbarkeit verbessert.
Die Metallbandabdeckung etwa schützt den Linearantrieb einerseits vor dem Eindringen von Schmutz oder Partikeln und verhindert andererseits die Partikelabgabe an die Umgebung. Damit eignen sich die Antriebe für Reinräume nach ISO 14644-1 von Klasse 1 bis 8. Das Fraunhofer-Institut für Produktionstechnik und Automatisierung hat dies geprüft und zertifiziert. Damit können Hersteller aus der Pharma- und Medizintechnik die Anforderungen an die Sauberkeit von Lineareinheiten erfüllen.
Nimmt die Fertigung für unterschiedliche Branchen in Reinräumen zu?
Definitiv! Nicht nur bei der Herstellung von Medizinprodukten und in der Halbleiterindustrie finden die Produktionsprozesse unter Reinraumbedingungen statt. Eine wachsende Anzahl von Produkten erfordert äußerst reine Produktionsbedingungen. Häufig ist es auch so, dass unsere Kunden nur im Reinraum fertigen können, um die Qualitätsanforderungen zu erfüllen.
Ein weiterer Messeschwerpunkt lag auf den Verstelleinheiten domiLINE. Was ist das Besondere, und können Sie typische Einsatzfälle nennen?
Mit diesem bewährten Einstell-Schlitten lassen sich zum Beispiel Messsysteme an jede mögliche Position manuell verschieben. Die Verstelleinheit ist modular aufgebaut und lässt sich leicht umrüsten. Mit den unterschiedlichen Schlittenbreiten ist der Anwender flexibel. Bei der kleinsten Version etwa sind ab Lager jeweils vier verschiedene Hübe von fünf bis 20, bei der größten von 25 bis 100 Millimetern lieferbar. Unser Kunde kann nicht nur Schlitten miteinander, sondern auch mit manuellen Dreheinheiten verbinden. Dafür haben wir die MDV-Serie im Programm, die in vier Größen erhältlich ist. Das Spiel der Schneckenverzahnung ist einstellbar und werkseitig schon optimal auf ein Minimum reduziert. Der Anwender profitiert von einer sehr hohen Wiederholgenauigkeit bei der Positionierung.
Spannend auf der Motek war das Portalsystem mit der Zahnriemenachse Modul 115/25 für die Handhabung von Paletten. Worauf kommt es dabei an?
Der Grundkörper des Moduls 115/25 zeichnet sich insbesondere durch eine hohe Biege- und Torsionssteifigkeit aus. Damit können Konstrukteure große Spannweiten umsetzen. Genau das ist beim Aufbau von Portalsystemen von Vorteil. Selbst bei hohen Belastungen und großen Hüben sind keine zusätzlichen Stützkonstruktionen erforderlich. Der Anwender spart nicht nur Kosten, er kann sein System auch deutlich schneller aufbauen als mit alternativen Lösungen. Es lassen sich hierbei Hübe bis 6,5 Meter realisieren.
Welche maximalen Gewichte lassen sich damit handhaben?
Die Handhabungsgewichte variieren je nach Applikation. Grundsätzlich ist unsere Zahnriemenachse Modul 115/25 jedoch für bis zu 150 Kilogramm ausgelegt. Die Achsen passen wir optimal für den individuellen Einsatz an. Wir garantieren so ein sicheres Positionieren auch bei hohen Gewichten.
Wie kam es zu dieser Entwicklung?
Unsere Kunden kamen immer häufiger mit Projekten auf uns zu, bei denen es darum ging, noch größere Gewichte handhaben zu können. Wir hatten lange Zeit in dieser Gewichtsklasse nichts im Programm. Der konsequente Schritt war eine Zahnriemenachse zu entwickeln, die ideal zu den bereits vorhandenen Positioniersystemen passt.
Nimmt das Palettenhandling grundsätzlich zu?
Das ist zumindest mein Eindruck. Paletten haben den Materialfluss und die Logistik in Deutschland und weltweit revolutioniert. Es gibt ja ganz unterschiedliche Paletten, je nach Budget und gewünschter Anwendung. Ihre strenge Normierung und international festgeschriebene Qualitätsstandards machen sie zum vielseitig einsetzbaren Ladungsträger. Ein professionelles Palettenhandling wird deshalb immer wichtiger.
Quelle: www.ief-werner.de
Schlagwörter: IEF Werner