Messgerätewerk in Italien steigert Effizienz dank Automatisierung der Logistik
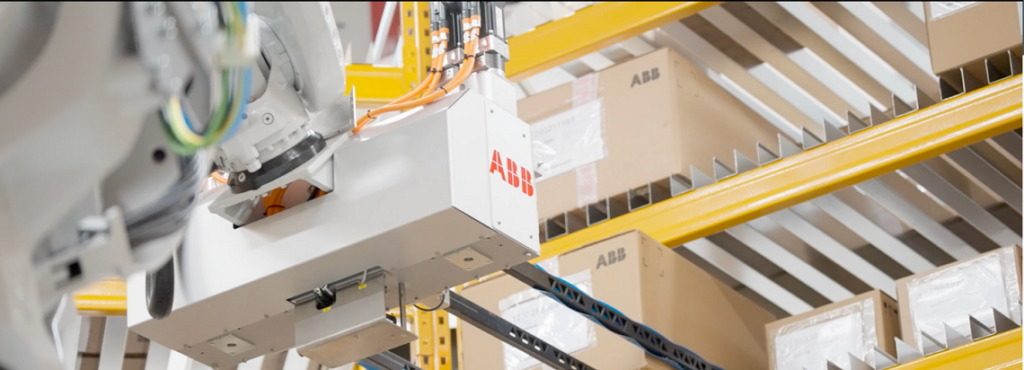
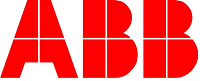
Die ABB-Division Mess- und Analysentechnik hat in ihrem Werk in Ossuccio, Italien, ein vollautomatisches Ein- und Auslagerungssystem implementiert, und so die Abläufe im Lager optimiert.
Mit Einführung einer Automatisierungslösung inklusive ABB-Roboter hat die ABB-Division Mess- und Analysentechnik die Umstellung des Logistikbetriebs in ihrem Messgerätewerk in Ossuccio, Italien, erfolgreich abgeschlossen. Die neue Lösung übernimmt alle Be- und Entladetätigkeiten im Lager, die bisher händisch ausgeführt wurden. Damit konnte die für die Zusammenstellung benötigte Zeit um 30 Prozent reduziert und die Gesamteffizienz der Logistik um 90 Prozent gesteigert werden.
Das ABB-Werk in Ossuccio ist auf die Herstellung von Druckmessumformern spezialisiert, die es Industrieunternehmen ermöglichen, die angewandte Druckkraft zu messen, zu überwachen und zu steuern. Die Druckmessung ist sowohl für die Sicherheit als auch für die Leistungsfähigkeit von grundlegender Bedeutung und spielt eine wichtige Rolle bei der digitalen Transformation. Das am Comer See in Italien gelegene Werk exportiert 90 Prozent seiner Produkte. Die jüngste Modernisierung verfolgte das Ziel, die Logistik auf ein neues Level zu heben und die Betriebseffizienz zu steigern.
„Wir wollten sowohl die Logistik am Standort Ossuccio sowie den gesamten Fertigungsprozess optimieren“, betont Mariafrancesca Madrigrano, Leiterin des Werks von ABB Mess- und Analysentechnik. „Um eine entsprechende Lösung zu finden, haben wir uns an unsere Kolleginnen und Kollegen von ABB Robotics gewandt. Das von ihnen implementierte System hat unsere Prozesse verbessert und geht einher mit unseren Zukunftsplänen.“
Die Lösung besteht aus zwei ABB OmniVance™ FlexBuffer™-Zellen. Diese sind durch ein Förderband verbunden und mit ABB-Robotern ausgestattet, um eine schnelle Auftragsabwicklung zu gewährleisten. FlexBuffer kombiniert Aufgaben wie Zwischenlagerung und Sequenzierung auf effektive Weise und bietet damit einen Vorteil gegenüber herkömmlichen Systemen. Die Variante von FlexBuffer für Mischartikel ermöglicht es Unternehmen, eine Vielzahl von Kartons unterschiedlicher Größen zu lagern, die alle mit demselben Robotergreifer gehandhabt werden. Weil auch die Regale flexibel bewegt werden können, lassen sich alle Kartons mit minimalem Platzverlust lagern.
„Was liegt näher, als die Leistungsfähigkeit einer ABB-Technologie in einem ABB-Werk unter Beweis zu stellen“, so Eduardo de Robbio, Segment und Portfolio Manager Consumer Industries bei ABB Robotics. „Die FlexBuffer-Zelle umfasst einen ABB-Roboter, Greifer und fortschrittliche Software. Sie leistet einen wichtigen Beitrag, den Output und die Effizienz zu steigern, und trägt den sich ständig verändernden Anforderungen und Kundenwünschen Rechnung. Die Implementierung bei ABB in Ossuccio unterstreicht die Modularität von FlexBuffer. Sie ermöglicht es, die für die Produktion benötigte Lagerkapazität optimal zur Verfügung zu stellen.“
Flexibler und effizienter Betrieb
FlexBuffer-Systeme sind über eine einzige Software-Suite einfach und schnell zu konfigurieren, zu installieren und zu warten. Das System verfügt zudem über digitale Schnittstellen zu verschiedenen Bereichen in der Werksplanung und den technischen Abteilungen. „Das Echtzeit-Tracking ermöglicht eine effiziente Planung und Abwicklung. Hinzu kommen Diagnosefunktionen, die wertvolle Erkenntnisse im Problemfall liefern“, sagt Eduardo de Robbio.
Prozess- und Kostenoptimierung
Durch Integration der ABB-Robotertechnologie in den Fertigungsprozess konnten die Betriebskosten, insbesondere in der Logistik, erheblich gesenkt werden. „Weil manuelle Tätigkeiten entfallen, ist es uns gelungen, den Produktionsfluss zu straffen und auch die Zeit für die Zusammenstellung um 30 Prozent zu reduzieren“, ergänzt Stefano Pizzetti, Factory Operations Manager. „Dies ist von entscheidender Bedeutung, da alle drei Minuten ein Stück bearbeitet wird. Das System verbessert unsere Effizienz und unsere Abläufe erheblich.“
Auch die Optimierung des Platzbedarfs ist eine wichtige Errungenschaft, die zur Steigerung des Durchsatzes beigetragen hat. Zu den weiteren Vorteilen gehört ein transparenter und fehlerfreier Prozess, der aufgrund der Integration mit der bestehenden SAP-Software eine bessere Rückverfolgbarkeit bietet. Und schließlich hat die Implementierung der neuen Lösung die Arbeitsbedingungen für die Mitarbeitenden verbessert. Denn die körperliche Belastung, die mit dem Heben schwerer Kisten einhergeht, ist deutlich gesunken. „Dies verbessert das Wohlbefinden unserer Mitarbeitenden und hilft uns, ein positives Arbeitsumfeld zu schaffen“, sagt Mariafrancesca Madrigrano.
Fokus auf kontinuierliche Verbesserung
Die Einführung des Systems war der Schlüssel zur kontinuierlichen Prozessoptimierung im Werk. „Mit der Implementierung der robotergestützten Automatisierungslösung haben wir die Weichen für weitere Innovationen gestellt, die uns helfen, noch besser auf spezifische Kundenanforderungen einzugehen und die Kundenzufriedenheit sicherzustellen“, resümiert Mariafrancesca Madrigrano. „Die Investition untermauert unser Engagement für stetige Verbesserung und Innovation.“
Automatisierung und Robotik waren entscheidend, um die Logistikabläufe zu verbessern und die Motivation der Belegschaft zu erhöhen. Das FlexBuffer-System führte zu einer 90-prozentigen Steigerung der Gesamteffizienz in der Logistik. Entgegen der Befürchtung, dass Arbeitsplätze abgebaut werden könnten, wurden Mitarbeitende in Bereichen eingesetzt, die zusätzliche Arbeitskräfte benötigten. „Die positiven Auswirkungen sind erheblich“, betont Stefano Pizzetti. „Es steht außer Frage, dass wir mit der neuen Lösung unsere Produkte schneller ausliefern können. Sie positioniert uns darüber hinaus als zuverlässigen und fortschrittlichen Branchenplayer.“
Quelle: www.abb.com
Schlagwörter: ABB